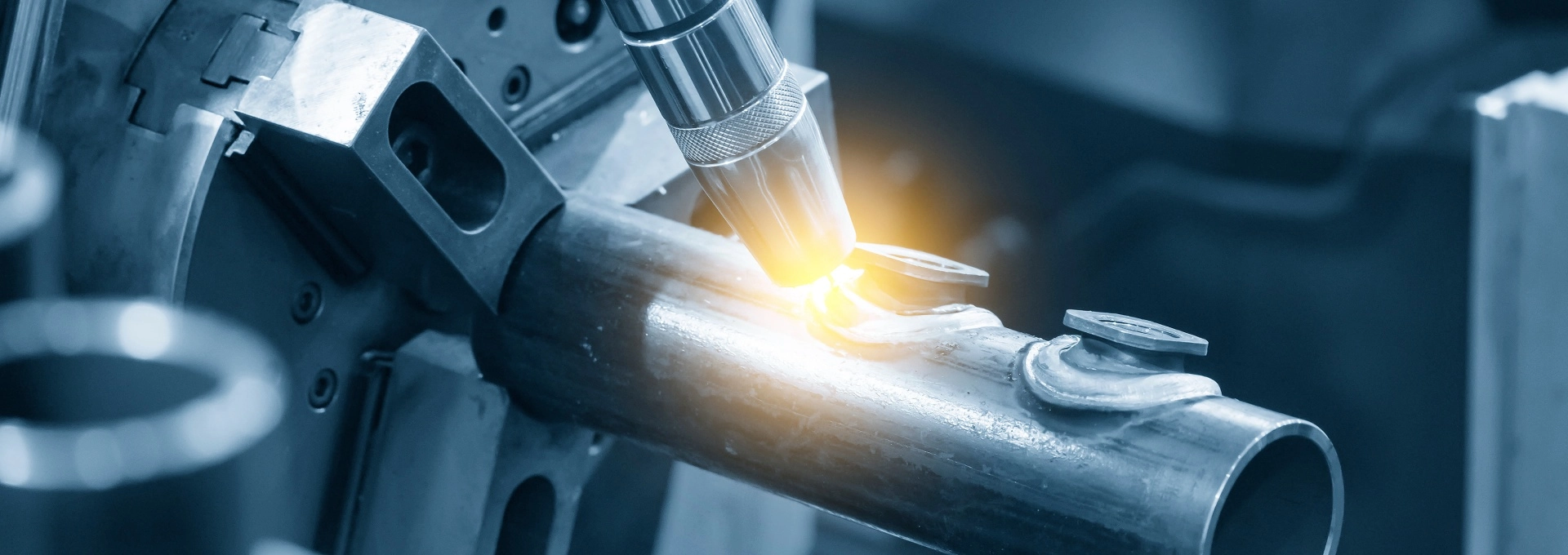
Friction stir welding (FSW) has emerged as a groundbreaking technique for joining dissimilar materials, addressing longstanding challenges in manufacturing and engineering. This solid-state process, invented at The Welding Institute (TWI) in 1991, utilizes mechanical stirring to create high-quality welds without melting the base materials. The ability to join dissimilar metals and alloys has opened up new possibilities in industries such as aerospace, automotive, and shipbuilding. Fsw welding offers numerous advantages over traditional fusion welding methods, including reduced distortion, improved mechanical properties, and the potential to join previously unweldable material combinations. As research and development in this field continue to advance, novel techniques and innovations are expanding the capabilities of FSW for dissimilar materials.
Advances in Friction Stir Welding Dissimilar Materials
The field of friction stir welding for dissimilar materials has witnessed remarkable progress in recent years, driven by the demand for lightweight, high-performance structures in various industries. Researchers and engineers have made significant strides in expanding the range of material combinations that can be successfully joined using FSW. These advancements have been facilitated by improvements in tool design, process parameters optimization, and a deeper understanding of the underlying mechanisms governing dissimilar material joints. The development of advanced FSW machines with enhanced process control capabilities has further contributed to the expansion of FSW applications for dissimilar materials. These machines allow for precise control of welding parameters such as rotational speed, traverse speed, and plunge depth, enabling the production of high-quality welds even with challenging material combinations.
One of the most notable advances in FSW for dissimilar materials has been the successful joining of aluminum alloys to steel, a combination that has long been considered difficult due to the formation of brittle intermetallic compounds. Researchers have developed innovative approaches to mitigate the formation of these detrimental phases, including the use of interlayer materials and specialized tool designs. For instance, the introduction of a zinc interlayer between aluminum and steel has been shown to improve weld strength and reduce the formation of intermetallic compounds. Additionally, the development of FSW tools with unique geometries, such as threaded and fluted pins, has enhanced material flow and mixing, leading to improved joint quality in dissimilar material welds.
Another significant advancement in FSW for dissimilar materials has been the joining of lightweight metals to high-temperature alloys, such as aluminum to titanium or magnesium to steel. These combinations are particularly attractive for aerospace and automotive applications, where weight reduction and high-temperature performance are critical. Researchers have developed specialized FSW techniques, including temperature-controlled FSW and hybrid FSW processes, to overcome the challenges associated with joining materials with vastly different melting points and thermal properties. These innovative approaches have enabled the production of high-strength, defect-free joints between dissimilar materials that were previously considered incompatible.
The application of FSW to join dissimilar polymers and polymer-metal combinations has also seen substantial progress. This has opened up new possibilities in the field of composite materials and lightweight structures. Researchers have successfully demonstrated the feasibility of joining thermoplastic composites to metals using FSW, creating hybrid structures with unique properties. The development of specialized FSW tools and process parameters tailored for polymer-based materials has been crucial in achieving these advancements. Furthermore, the use of FSW for joining dissimilar polymers has shown promise in applications such as pipe joining and automotive components, offering advantages over traditional adhesive bonding techniques.
Challenges Overcome with Friction Stir Welding Techniques
The successful implementation of friction stir welding for dissimilar materials has required overcoming numerous challenges inherent to joining materials with disparate properties. These challenges have necessitated the development of innovative techniques and approaches to ensure the production of high-quality, reliable joints. The primary obstacles faced in FSW of dissimilar materials include material incompatibility, differences in melting points and thermal properties, formation of brittle intermetallic compounds, and achieving optimal material flow and mixing. Addressing these challenges has been the focus of extensive research and development efforts in the field of FSW.
Addressing Material Incompatibility Issues
Material incompatibility has been one of the most significant challenges in friction stir welding of dissimilar materials. The differences in physical and chemical properties between the materials being joined can lead to poor weld quality, reduced mechanical properties, and the formation of detrimental phases at the joint interface. To address this challenge, researchers have developed several innovative approaches. One such approach involves the use of interlayer materials to promote compatibility between dissimilar materials. For example, in the case of aluminum-steel joints, the introduction of a zinc or nickel interlayer has been shown to improve weldability and joint strength by mitigating the formation of brittle intermetallic compounds.
Another technique used to overcome material incompatibility is the application of surface treatments or coatings to one or both of the materials being joined. These treatments can modify the surface properties of the materials, promoting better bonding and reducing the formation of undesirable phases. For instance, in the case of joining aluminum to titanium, the application of a thin copper coating on the titanium surface has been demonstrated to enhance weld quality and mechanical properties. Additionally, researchers have explored the use of functionally graded materials (FGMs) as transition layers between dissimilar materials. These FGMs provide a gradual change in composition and properties across the joint, reducing stress concentrations and improving overall joint performance.
The development of specialized FSW tool designs has also played a crucial role in addressing material incompatibility issues. Tools with complex geometries, such as threaded and fluted pins, have been shown to enhance material flow and mixing, leading to improved joint quality in dissimilar material welds. For example, tools with scrolled shoulders have been found to be particularly effective in joining aluminum alloys to magnesium alloys, as they promote better material flow and reduce the formation of defects at the joint interface. Furthermore, the use of stationary shoulder FSW tools has shown promise in joining materials with significantly different melting points, as it allows for better control of heat input and material flow during the welding process.
Optimizing Process Parameters for Dissimilar Joints
The optimization of process parameters is critical for achieving high-quality friction stir welds in dissimilar materials. The complex interactions between different materials during FSW necessitate careful selection and control of welding parameters to ensure optimal joint properties. Key process parameters that require optimization include tool rotational speed, traverse speed, plunge depth, and tool tilt angle. These parameters significantly influence heat generation, material flow, and mixing behavior during the welding process, ultimately affecting the microstructure and mechanical properties of the resulting joint. Researchers have employed various approaches to optimize FSW process parameters for dissimilar materials, including experimental design techniques, statistical analysis, and computational modeling.
One effective method for optimizing process parameters is the use of design of experiments (DOE) techniques, such as response surface methodology (RSM) and Taguchi methods. These approaches allow for systematic evaluation of the effects of multiple process parameters on weld quality and mechanical properties.
Advanced computational modeling techniques have also been employed to optimize FSW process parameters for dissimilar materials. Finite element analysis (FEA) and computational fluid dynamics (CFD) simulations have been used to predict temperature distributions, material flow patterns, and stress states during FSW of dissimilar materials. These models provide valuable insights into the complex phenomena occurring during the welding process, enabling researchers to identify optimal parameter combinations without the need for extensive experimental trials. For instance, a CFD model developed for FSW of aluminum to steel accurately predicted the formation of intermetallic compounds and helped identify process parameters that minimized their occurrence.
The development of closed-loop control systems for FSW machines has further enhanced the ability to optimize and maintain process parameters during welding of dissimilar materials. These systems utilize real-time feedback from sensors monitoring parameters such as force, torque, and temperature to adjust welding parameters dynamically. This approach allows for more consistent weld quality and improved adaptability to variations in material properties or geometries. For example, a force-controlled FSW system developed for joining aluminum to magnesium alloys demonstrated improved weld quality and reduced defect formation compared to conventional position-controlled systems.
Mitigating Intermetallic Compound Formation
The formation of brittle intermetallic compounds (IMCs) at the joint interface is a significant challenge in friction stir welding of dissimilar materials, particularly when joining metals with vastly different chemical properties. These IMCs can severely degrade the mechanical properties and corrosion resistance of the welded joint, leading to premature failure. Addressing this challenge has been a primary focus of research in FSW of dissimilar materials, with several innovative approaches developed to mitigate IMC formation. One effective strategy involves controlling the heat input and cooling rate during the welding process to limit the growth of IMCs. This can be achieved through careful optimization of welding parameters such as tool rotational speed and traverse speed.
The use of interlayer materials has proven to be a highly effective method for mitigating IMC formation in FSW of dissimilar materials. Interlayers can act as diffusion barriers, limiting the direct contact between incompatible materials and reducing the formation of brittle phases. For example, in aluminum-steel joints, the introduction of a zinc interlayer has been shown to significantly reduce the thickness of the IMC layer and improve joint strength. Similarly, the use of a copper interlayer in aluminum-titanium joints has demonstrated improved weldability and reduced IMC formation. Researchers have also explored the use of multi-layer interlayers, such as Al-Cu-Ni systems, which provide a gradual transition in composition across the joint interface, further minimizing IMC formation.
Another innovative approach to mitigating IMC formation is the application of post-weld heat treatments (PWHT) tailored for dissimilar material joints. These heat treatments can modify the microstructure and composition of the joint interface, promoting the formation of more favorable phases and reducing the presence of brittle IMCs.
Innovative Approaches to Dissimilar Material Welding
The field of friction stir welding for dissimilar materials has witnessed the development of numerous innovative approaches aimed at expanding the capabilities of the process and overcoming the inherent challenges associated with joining disparate materials. These novel techniques have emerged from extensive research efforts and industrial collaborations, addressing specific limitations of conventional FSW methods when applied to dissimilar material combinations. The innovative approaches encompass a wide range of modifications to the FSW process, including tool design, process variants, and the integration of complementary technologies. These advancements have significantly broadened the scope of materials that can be successfully joined using FSW, opening up new possibilities for lightweight, high-performance structures in various industries.
Hybrid Friction Stir Welding Methods
Hybrid friction stir welding methods have emerged as a promising approach to enhance the capabilities of FSW for joining dissimilar materials. These techniques combine FSW with other welding or material processing methods to achieve improved joint properties and overcome specific challenges associated with certain material combinations. One notable hybrid approach is the combination of FSW with ultrasonic vibration, known as ultrasonic-assisted friction stir welding (UA-FSW). In this method, high-frequency ultrasonic vibrations are applied to the FSW tool or workpiece during the welding process, resulting in enhanced material flow and mixing, reduced welding forces, and improved joint quality.
Another innovative hybrid technique is laser-assisted friction stir welding (LA-FSW), which integrates a laser heat source with the FSW process. The laser is used to preheat the material ahead of the FSW tool, softening the workpiece and reducing the forces required for welding. This approach has shown particular promise in joining high-strength materials and dissimilar combinations with significant differences in melting points. For example, LA-FSW has been successfully applied to join aluminum alloys to titanium alloys, achieving improved weld quality and reduced defect formation compared to conventional FSW. The preheating effect of the laser also allows for higher welding speeds, potentially increasing productivity in industrial applications.
Electrically-assisted friction stir welding (EA-FSW) is another hybrid method that has demonstrated potential for improving the weldability of dissimilar materials. In this technique, an electric current is passed through the workpiece or tool during the FSW process, generating localized resistive heating. This additional heat input can enhance material flow and plasticity, particularly beneficial when joining materials with high melting points or significantly different thermal properties. EA-FSW has been successfully applied to join aluminum to steel and magnesium to steel, showing improvements in joint strength and reductions in defect formation compared to conventional FSW.
The integration of induction heating with FSW has also been explored as a hybrid approach for dissimilar material welding. Induction-assisted friction stir welding (IA-FSW) utilizes an induction coil to preheat the workpiece ahead of the FSW tool, providing better control over the temperature distribution during welding. This method has shown promise in joining thermoplastics to metals, where precise temperature control is critical to achieving good bonding without degrading the polymer. Additionally, IA-FSW has been applied to joining high-temperature alloys, where preheating can significantly reduce tool wear and improve overall weld quality.
Innovative Approaches to Dissimilar Material Welding
Friction stir welding for dissimilar materials has witnessed the development of numerous innovative techniques aimed at expanding process capabilities and overcoming challenges associated with joining disparate materials. These novel approaches have emerged from extensive research efforts and industrial collaborations, addressing specific limitations of conventional FSW methods when applied to dissimilar material combinations. The advancements encompass a wide range of modifications to the FSW process, including tool design, process variants, and the integration of complementary technologies. These innovations have significantly broadened the scope of materials that can be successfully joined using FSW, creating new possibilities for lightweight, high-performance structures in various industries.
Hybrid Friction Stir Welding Methods
Hybrid friction stir welding methods combine FSW with other welding or material processing techniques to achieve improved joint properties and overcome specific challenges associated with certain material combinations. One notable approach involves the integration of ultrasonic vibration with FSW, known as ultrasonic-assisted friction stir welding (UA-FSW). In this method, high-frequency ultrasonic vibrations are applied to the FSW tool or workpiece during the welding process, resulting in enhanced material flow and mixing, reduced welding forces, and improved joint quality.
Laser-assisted friction stir welding (LA-FSW) represents another innovative hybrid technique that incorporates a laser heat source into the FSW process. The laser preheats the material ahead of the FSW tool, softening the workpiece and reducing the forces required for welding. This approach has demonstrated particular efficacy in joining high-strength materials and dissimilar combinations with significant differences in melting points. For instance, LA-FSW has been successfully applied to join aluminum alloys to titanium alloys, achieving improved weld quality and reduced defect formation compared to conventional FSW. The preheating effect of the laser also facilitates higher welding speeds, potentially increasing productivity in industrial applications.
Electrically-assisted friction stir welding (EA-FSW) has emerged as a promising hybrid method for improving the weldability of dissimilar materials. This technique involves passing an electric current through the workpiece or tool during the FSW process, generating localized resistive heating. The additional heat input enhances material flow and plasticity, proving particularly beneficial when joining materials with high melting points or significantly different thermal properties. EA-FSW has been successfully applied to join aluminum to steel and magnesium to steel, demonstrating improvements in joint strength and reductions in defect formation compared to conventional FSW.
The integration of induction heating with FSW, known as induction-assisted friction stir welding (IA-FSW), utilizes an induction coil to preheat the workpiece ahead of the FSW tool, providing better control over the temperature distribution during welding. This method has shown promise in joining thermoplastics to metals, where precise temperature control is critical to achieving good bonding without degrading the polymer. Additionally, IA-FSW has been applied to joining high-temperature alloys, where preheating can significantly reduce tool wear and improve overall weld quality.
Multi-Pass Friction Stir Welding Strategies
Multi-pass friction stir welding strategies have emerged as effective techniques for improving the quality and properties of dissimilar material joints. These approaches involve performing multiple FSW passes along the same weld line or in different configurations to achieve specific microstructural and mechanical property enhancements. The implementation of multi-pass FSW strategies has proven particularly beneficial in addressing challenges associated with thick-section welding and the joining of materials with significantly different properties.
One common multi-pass FSW strategy involves performing multiple passes along the same weld line, with each subsequent pass refining the microstructure and improving the homogeneity of the weld zone. This approach has been successfully applied to joining thick aluminum plates, where a single pass may not provide sufficient material mixing and property homogenization throughout the weld thickness. Research has shown that multi-pass FSW can lead to grain refinement, improved distribution of strengthening precipitates, and enhanced mechanical properties compared to single-pass welds.
Another multi-pass strategy involves the use of alternating tool rotation directions between passes, known as reversing multi-pass FSW. This technique has been shown to promote more uniform material flow and mixing, particularly beneficial in joining dissimilar materials with significant property differences. By alternating the rotation direction, the asymmetry of material flow typically observed in FSW can be balanced, leading to improved joint quality and reduced defect formation.
Overlapping multi-pass FSW represents another innovative approach, particularly useful for joining wide plates or creating large-area dissimilar material joints. In this strategy, multiple parallel weld passes are performed with a certain degree of overlap between adjacent passes. This technique ensures complete joining across the entire width of the plates and can lead to improved mechanical properties due to the repeated thermomechanical processing of the overlap regions. Research on overlapping multi-pass FSW of dissimilar aluminum alloys has demonstrated improvements in hardness uniformity and tensile strength compared to single-pass welds of the same materials.
Friction Stir Welding with Interlayers
Friction stir welding with interlayers represents an innovative approach to joining dissimilar materials, addressing challenges related to material incompatibility and the formation of detrimental intermetallic compounds. This technique involves the introduction of an intermediate layer between the materials to be joined, facilitating better bonding and mitigating the formation of brittle phases at the joint interface. The selection of appropriate interlayer materials and their integration into the FSW process have been the subject of extensive research, yielding promising results for various dissimilar material combinations.
One of the primary advantages of using interlayers in FSW of dissimilar materials is the ability to create a gradual transition in composition and properties across the joint interface. This gradual transition helps to reduce stress concentrations and improve the overall mechanical performance of the welded joint
The effectiveness of interlayers in FSW of dissimilar materials extends beyond aluminum-steel combinations. Research has demonstrated the benefits of using copper interlayers in joining aluminum to titanium alloys, a material combination of particular interest for aerospace applications. The copper interlayer promotes the formation of more ductile intermetallic phases, such as Al2Cu and Ti2Cu, instead of the brittle TiAl3 phase typically observed in direct aluminum-titanium joints.
Multi-layer interlayers have also been explored as a means of further enhancing the properties of dissimilar material FSW joints. These systems typically consist of two or more layers of different materials, each chosen to provide specific benefits in terms of diffusion control, phase formation, or mechanical properties. For instance, an Al-Cu-Ni multi-layer interlayer system has been investigated for joining magnesium alloys to aluminum alloys. The aluminum layer promotes bonding with the magnesium substrate, while the nickel layer acts as a diffusion barrier to limit the formation of Mg-Al intermetallic compounds. The copper layer serves as a transition between the aluminum and nickel, improving overall interlayer stability. Experimental results have shown that FSW joints produced using this multi-layer interlayer system exhibit superior strength and ductility compared to both direct joints and those produced with single-layer interlayers.
Microstructural Evolution in Dissimilar Friction Stir Welds
The microstructural evolution in dissimilar friction stir welds plays a crucial role in determining the mechanical properties and overall performance of the joint. The complex thermomechanical processes involved in FSW of dissimilar materials result in unique microstructural features that differ significantly from those observed in similar material welds. Understanding these microstructural changes is essential for optimizing welding parameters and predicting joint behavior under various loading conditions. Research in this area has focused on characterizing the distinct zones within dissimilar FSW joints, including the stir zone, thermomechanically affected zone (TMAZ), and heat-affected zone (HAZ), as well as the interfaces between these regions.
The stir zone of dissimilar FSW joints exhibits a complex microstructure resulting from the intense plastic deformation and material mixing during the welding process. In many cases, a layered or banded structure is observed, with alternating regions of the two base materials. The degree of material mixing and the resulting microstructure are heavily influenced by the welding parameters, tool design, and material properties.
The formation of intermetallic compounds (IMCs) at the interface between dissimilar materials is a critical aspect of microstructural evolution in FSW joints. These IMCs can significantly affect joint properties, often leading to embrittlement and reduced mechanical performance if not properly controlled. Advanced characterization techniques, such as transmission electron microscopy (TEM) and atom probe tomography (APT), have been employed to study the formation and distribution of IMCs in dissimilar FSW joints. A detailed TEM analysis of an aluminum-steel FSW joint revealed the presence of nanoscale Fe-Al IMCs at the interface, with their composition and crystal structure varying depending on the local temperature and deformation history during welding. The thickness of the IMC layer was found to be inversely proportional to the welding speed, with faster welding speeds resulting in thinner and more discontinuous IMC layers.
Grain refinement is another important microstructural feature observed in the stir zone of dissimilar FSW joints. The severe plastic deformation and dynamic recrystallization processes during FSW typically result in a fine-grained microstructure in this region. However, the extent of grain refinement can vary significantly between the two materials being joined due to differences in their recrystallization behavior and thermal properties.
The thermomechanically affected zone (TMAZ) in dissimilar FSW joints presents unique microstructural characteristics due to the different responses of the base materials to the thermal and mechanical cycles during welding. This region often exhibits a gradient in grain size and orientation, with the microstructure transitioning from the highly deformed stir zone to the less affected base material. In some cases, partial recrystallization may occur in the TMAZ, leading to a mix of deformed and recrystallized grains. A detailed electron backscatter diffraction (EBSD) analysis of the TMAZ in an aluminum-copper FSW joint revealed a gradual change in grain orientation and size across this region, with the aluminum side showing a more pronounced recrystallization compared to the copper side due to its lower recrystallization temperature.